Onsite Support
VALUE CHAIN >>>
Expert support to optimize operational efficiency in Production, Logistics, Purchasing and Procurement and Production Engineering.
Onsite Support
CADENA DE VALOR >>>
Expert support to optimize operational efficiency in Production, Logistics, Purchasing and Procurement and Production Engineering.
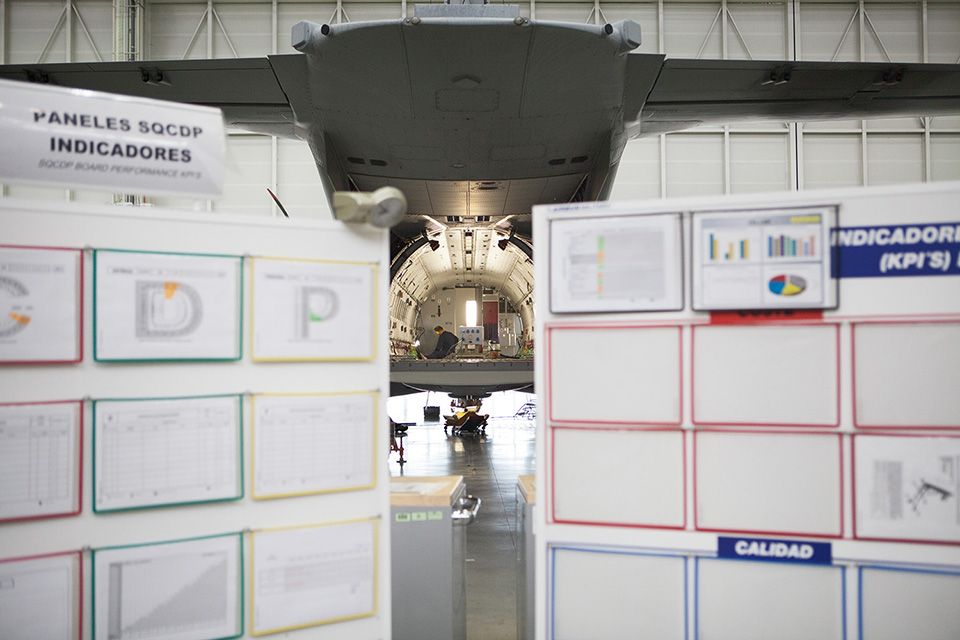
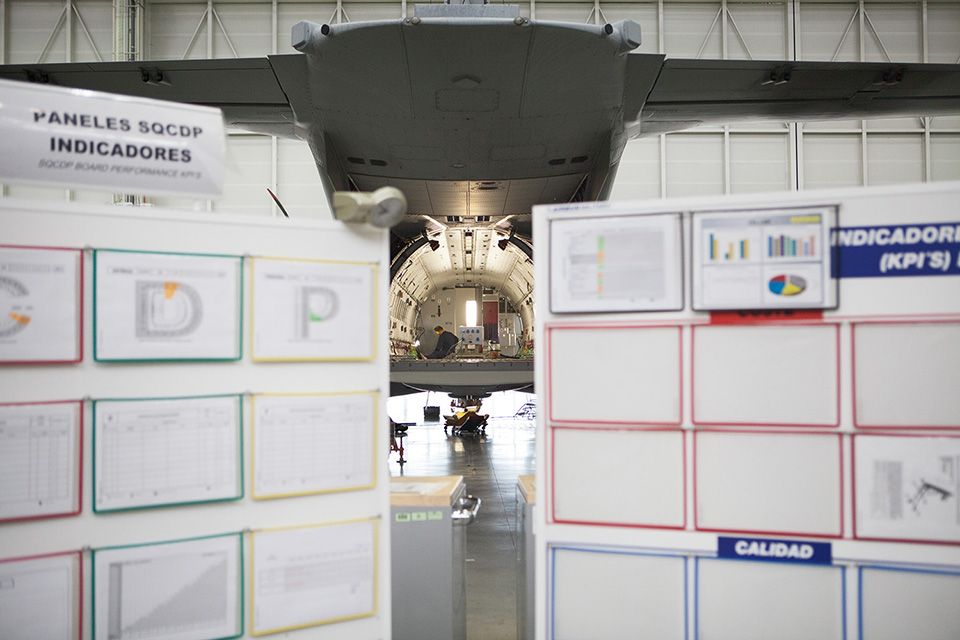
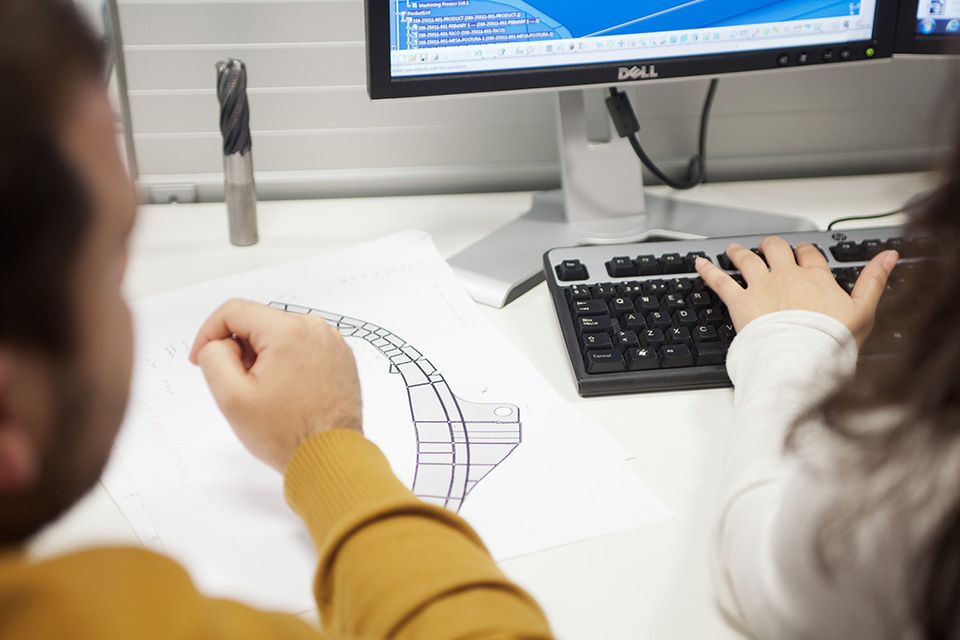
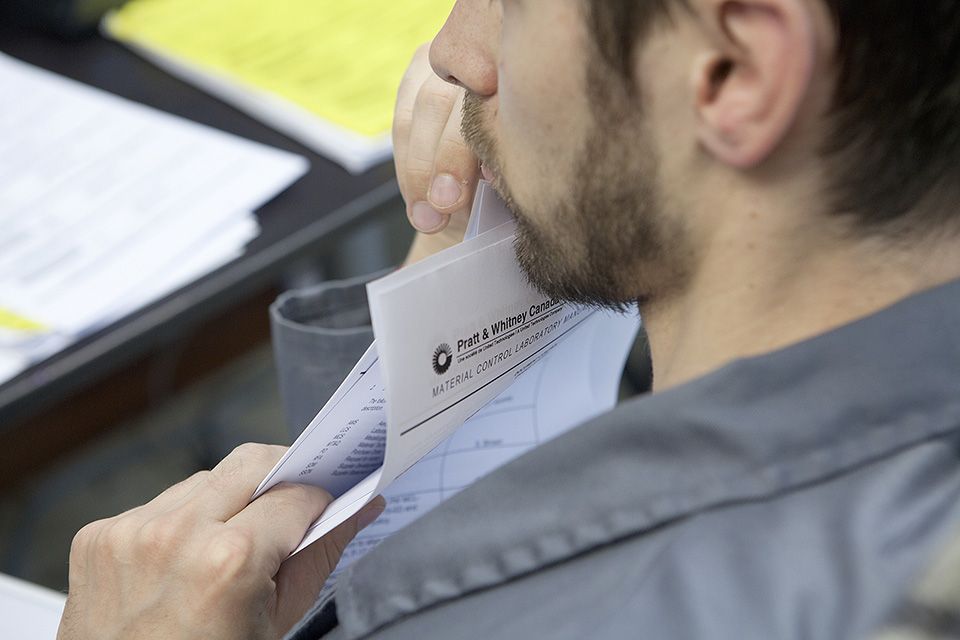
SERVICE SCOPE
TORSESA's on-site support service is designed to provide direct and continuous assistance in the daily operations of production plants, covering different departments that require specialized support. This approach allows the effective integration of TORSESA personnel into the working environment, facilitating the identification and resolution of problems in real time. The constant presence of experts on site ensures that high standards of efficiency and quality are maintained in all operational activities.
TORSESA personnel are responsible for managing a variety of critical functions, including receiving, warehousing, replenishment and product shipping. Their expertise in planning and scheduling allows them to optimize workflow and ensure that resources are used effectively. In addition, inventory control becomes a more agile and accurate task, helping to minimize costs and maximize product availability at the right time.
The implementation of optimization methodologies and the evaluation of appropriate technologies are an integral part of the on-site support. The TORSESA team not only takes care of the commissioning and refurbishment of warehouses, but also conducts periodic audits to evaluate process efficiency and compliance with operating procedures. This allows us to identify areas for improvement and propose corrective actions that are immediately implemented, ensuring a cycle of continuous improvement in plant operations.
In addition, the service includes a training and development component where TORSESA personnel train internal personnel in the use of new technologies and best practices. This training is essential to foster a proactive and adaptive work environment, where skills related to warehouse management and operations are promoted. By incorporating automation and digitalization into processes, such as the implementation of WMS systems and ERP integration, significant inventory optimization and improvement in overall plant operational efficiency is achieved.
APPLICATION AREAS
The possible scope of TORSESA's on-site support service covers several key areas of plant operation, each with its own specific needs and challenges. These areas are described below:
Logistics
In this area, TORSESA personnel focus on optimizing inventory management, receiving and shipping of products. This includes the implementation of inventory control systems, the improvement of storage processes and the efficient planning of distribution routes. The presence of logistic experts allows a quick response to any inconveniences that may arise, ensuring that operations remain smooth and efficient.
Production
In the production area, on-site support is focused on improving the efficiency of production lines, resource management and the implementation of continuous improvement methodologies such as Lean and Six Sigma. TORSESA personnel can help identify bottlenecks in the production process and propose solutions to optimize the workflow, reduce downtime and improve the quality of the final product.
Purchasing and procurement
In the area of purchasing, TORSESA's support can include optimizing supplier management, evaluating costs and improving procurement processes. This involves working closely with the department to ensure that purchases are made efficiently and that adequate inventory levels are maintained, avoiding both overstocking and understocking.
Manufacturing Engineering
On the engineering side, on-site support can include the implementation of new technologies and the improvement of existing processes. TORSESA personnel can collaborate on engineering projects to optimize plant design, equipment selection and integration of automated systems. This not only improves operational efficiency, but also contributes to innovation and adaptation of the plant to market demands.
ALCANCE DEL SERVICIO
TORSESA's on-site support service is designed to provide direct and continuous assistance in the daily operations of production plants, covering different departments that require specialized support. This approach allows the effective integration of TORSESA personnel into the working environment, facilitating the identification and resolution of problems in real time. The constant presence of experts on site ensures that high standards of efficiency and quality are maintained in all operational activities.
TORSESA personnel are responsible for managing a variety of critical functions, including receiving, warehousing, replenishment and product shipping. Their expertise in planning and scheduling allows them to optimize workflow and ensure that resources are used effectively. In addition, inventory control becomes a more agile and accurate task, helping to minimize costs and maximize product availability at the right time.
The implementation of optimization methodologies and the evaluation of appropriate technologies are an integral part of the on-site support. The TORSESA team not only takes care of the commissioning and refurbishment of warehouses, but also conducts periodic audits to evaluate process efficiency and compliance with operating procedures. This allows us to identify areas for improvement and propose corrective actions that are immediately implemented, ensuring a cycle of continuous improvement in plant operations.
In addition, the service includes a training and development component where TORSESA personnel train internal personnel in the use of new technologies and best practices. This training is essential to foster a proactive and adaptive work environment, where skills related to warehouse management and operations are promoted. By incorporating automation and digitalization into processes, such as the implementation of WMS systems and ERP integration, significant inventory optimization and improvement in overall plant operational efficiency is achieved.
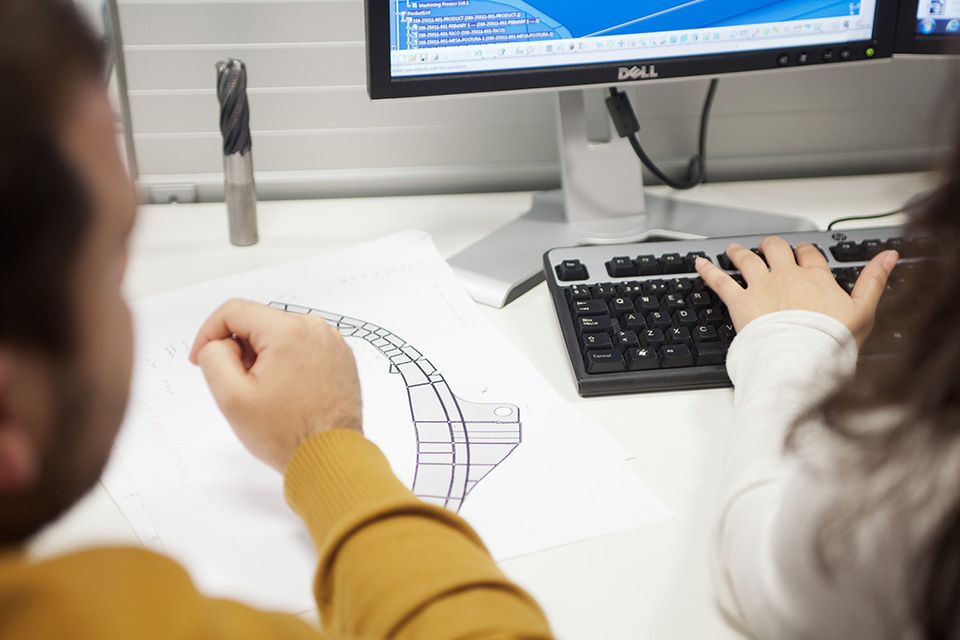
Áreas de Aplicación
The possible scope of TORSESA's on-site support service covers several key areas of plant operation, each with its own specific needs and challenges. These areas are described below:
Logistics
In this area, TORSESA personnel focus on optimizing inventory management, receiving and shipping of products. This includes the implementation of inventory control systems, the improvement of storage processes and the efficient planning of distribution routes. The presence of logistic experts allows a quick response to any inconveniences that may arise, ensuring that operations remain smooth and efficient.
Production
In the production area, on-site support is focused on improving the efficiency of production lines, resource management and the implementation of continuous improvement methodologies such as Lean and Six Sigma. TORSESA personnel can help identify bottlenecks in the production process and propose solutions to optimize the workflow, reduce downtime and improve the quality of the final product.
Purchasing and procurement
In the area of purchasing, TORSESA's support can include optimizing supplier management, evaluating costs and improving procurement processes. This involves working closely with the department to ensure that purchases are made efficiently and that adequate inventory levels are maintained, avoiding both overstocking and understocking.
Manufacturing Engineering
On the engineering side, on-site support can include the implementation of new technologies and the improvement of existing processes. TORSESA personnel can collaborate on engineering projects to optimize plant design, equipment selection and integration of automated systems. This not only improves operational efficiency, but also contributes to innovation and adaptation of the plant to market demands.
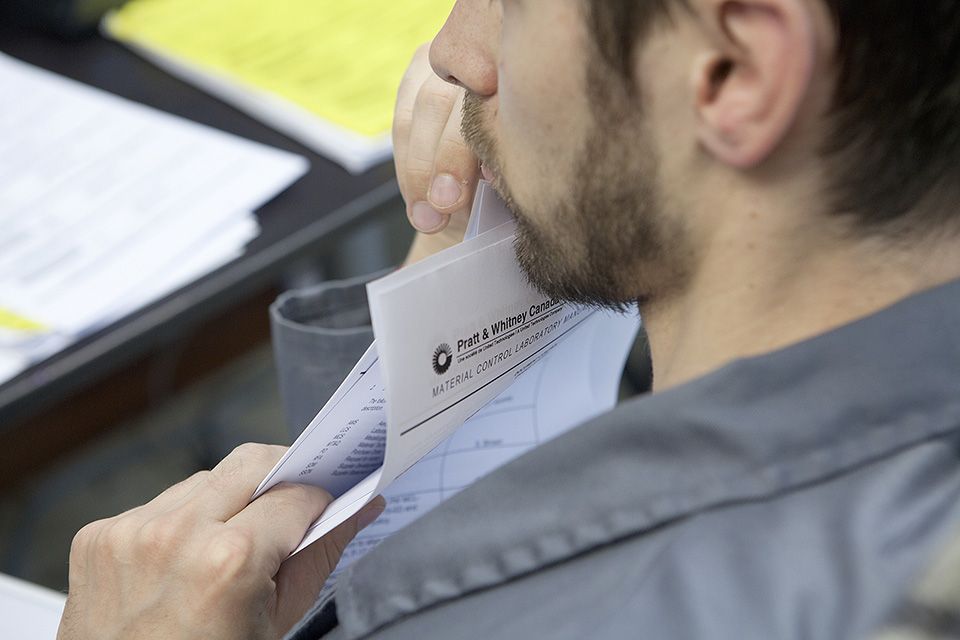
BENEFITS
-
Operational Efficiency
Streamline processes, reduce costs, and increase operational capacity.
-
Corporate Sustainability
Responsible sourcing and procurement practices.
-
Personnel Training
Improving quality of work and adapting to new technologies.
-
Adaptability
Respond quickly to changes in the operating environment.
BENEFICIOS
-
Operational Efficiency
Streamline processes, reduce costs, and increase operational capacity.
-
Corporate Sustainability
Responsible sourcing and procurement practices.
-
Personnel Training
Improving quality of work and adapting to new technologies.
-
Adaptability
Respond quickly to changes in the operating environment.
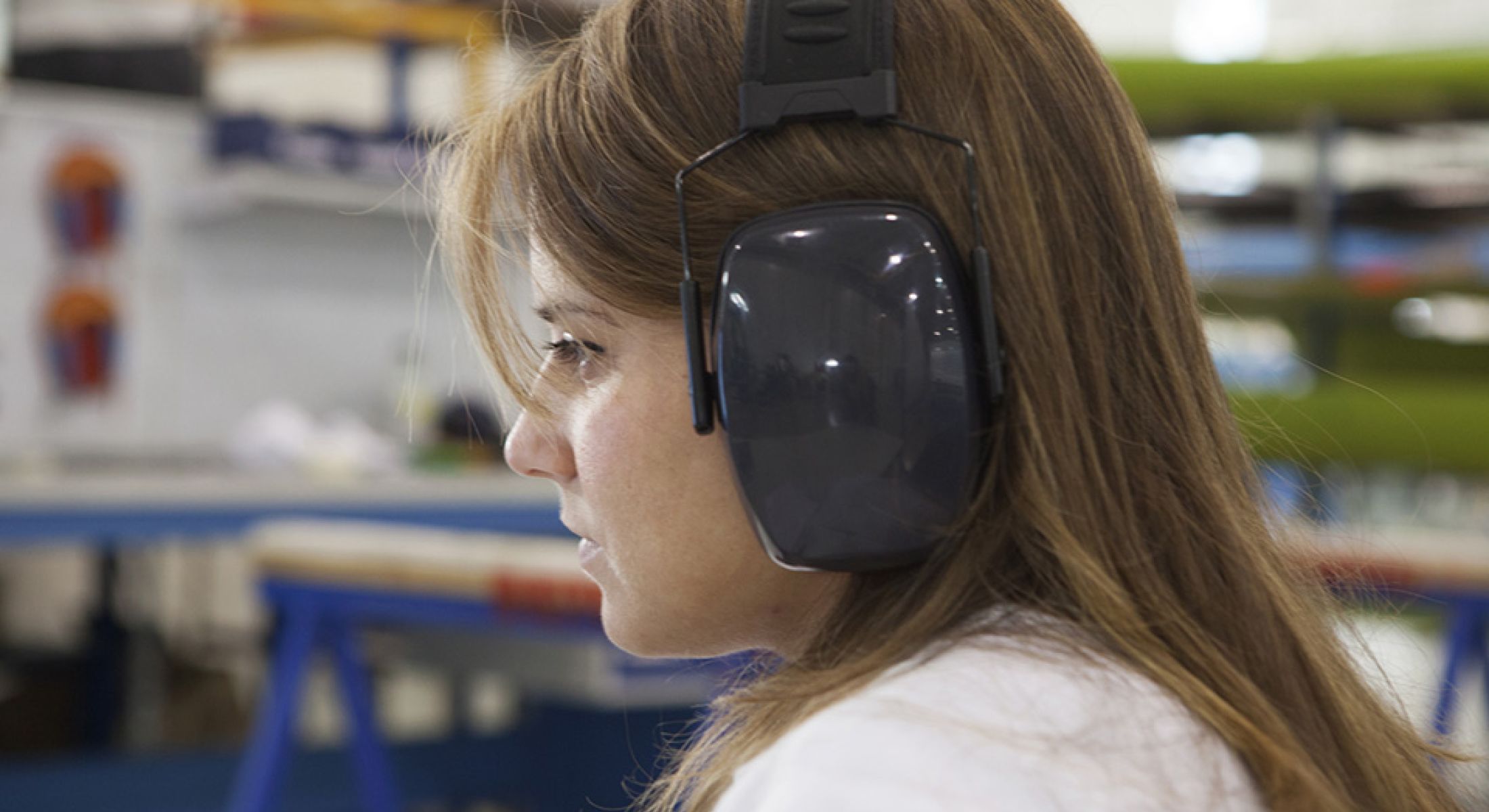
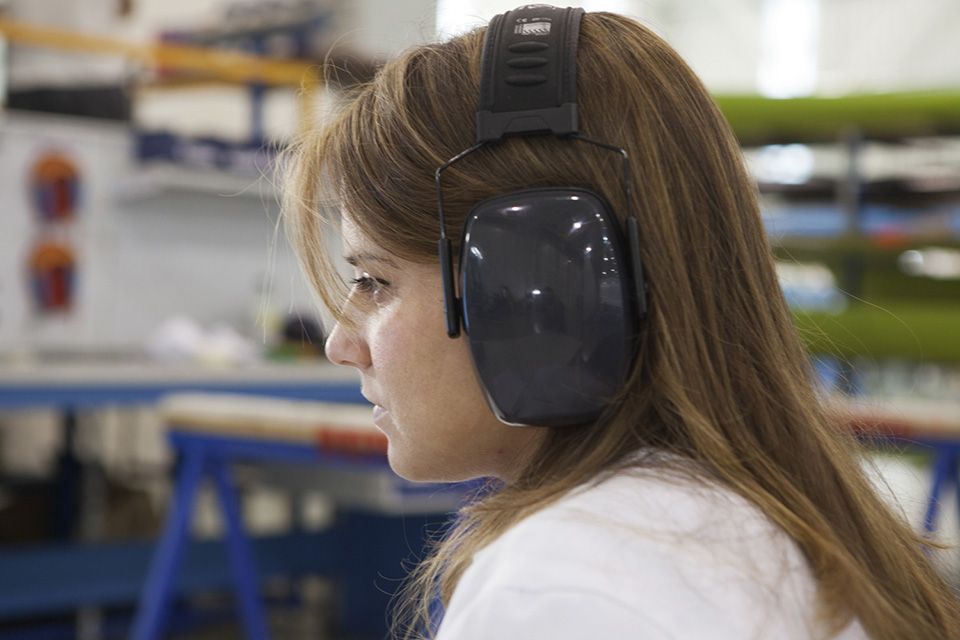