Kanban Solutions
VALUE CHAIN >>>
Logistics process improvement to ensure the availability of resources and higher responsiveness to production requirements.
Kanban Solutions
CADENA DE VALOR >>>
Logistics process improvement to ensure the availability of resources and higher responsiveness to production requirements.
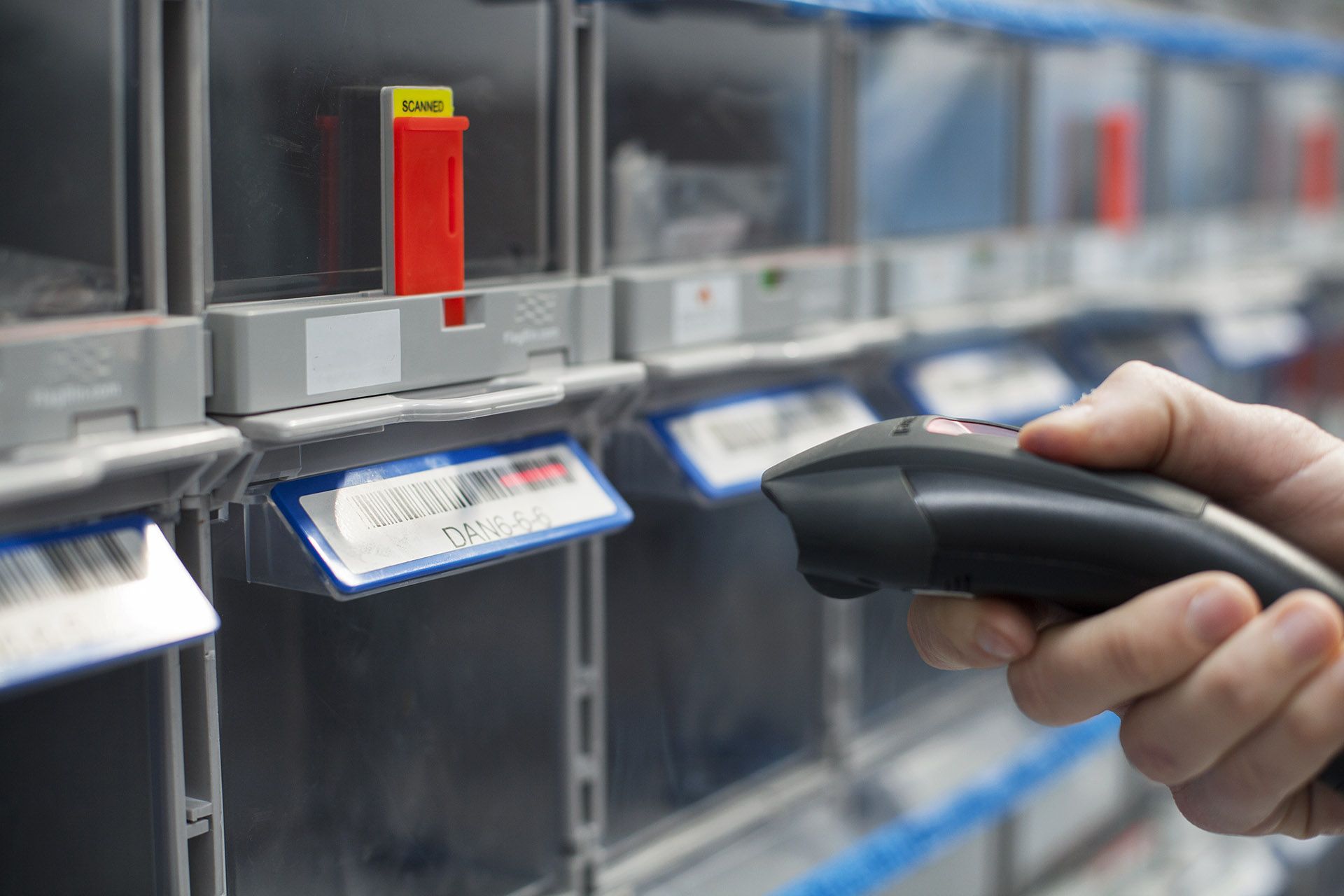
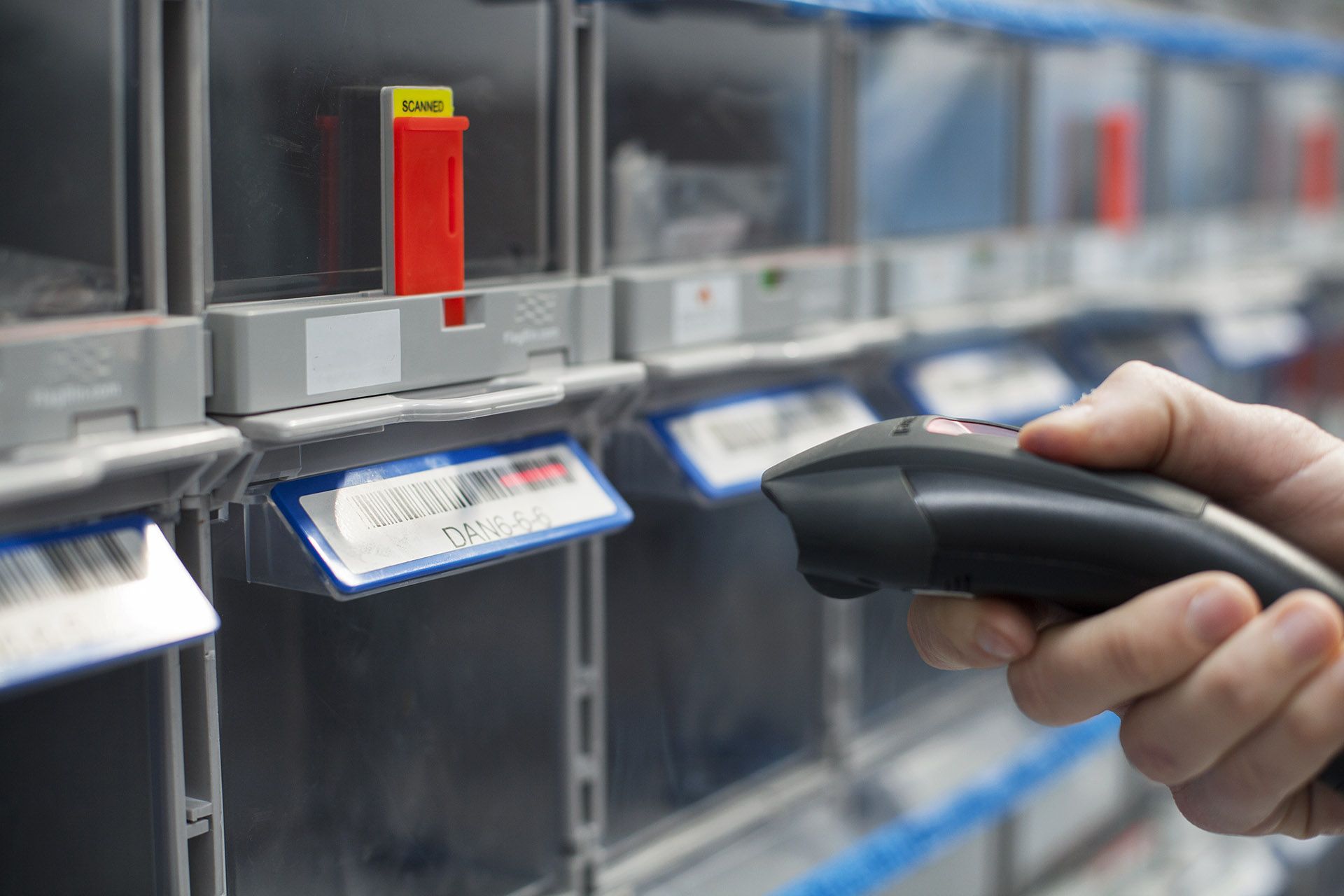
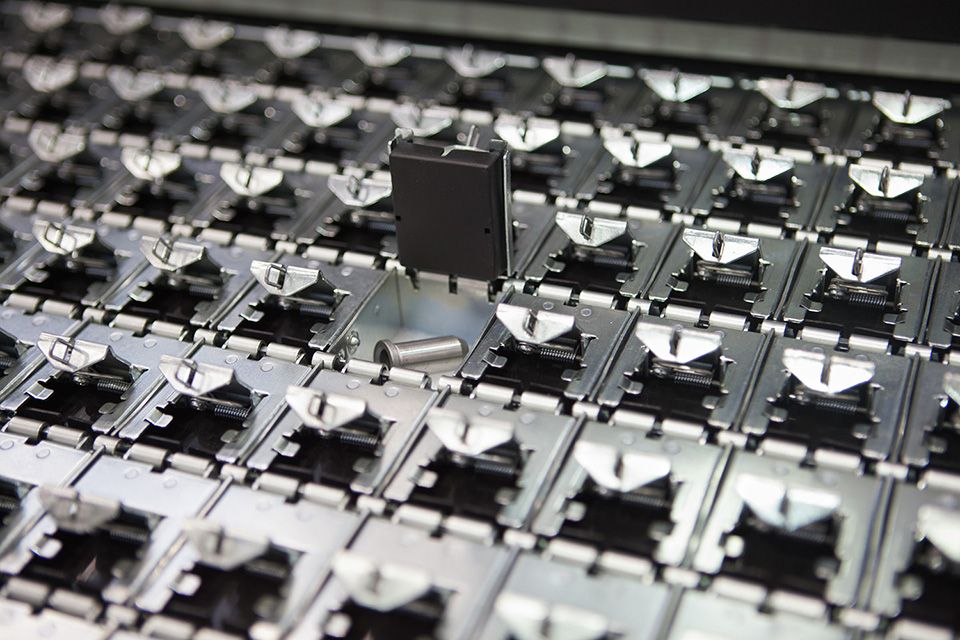
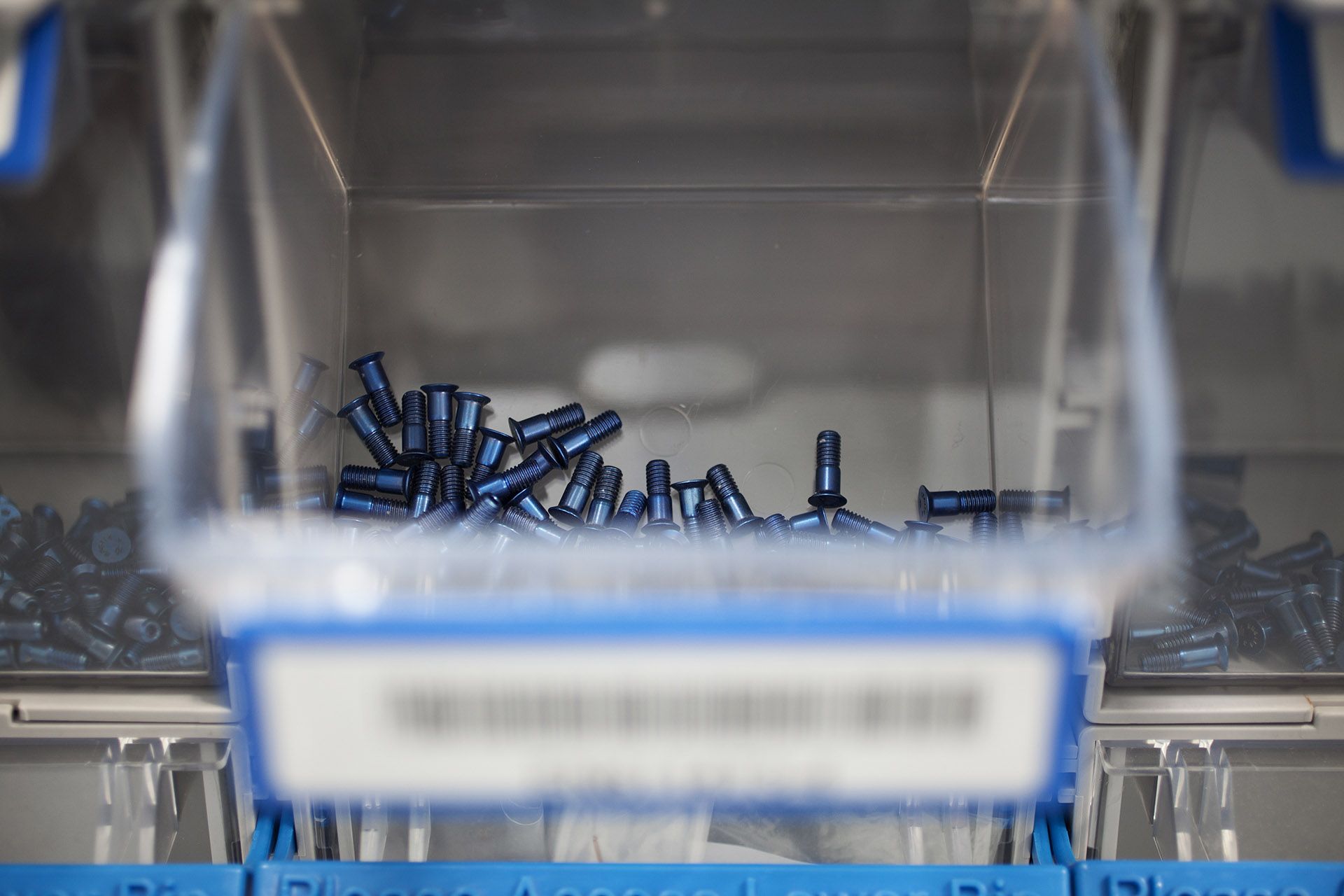
SERVICE SCOPE
Optimization of internal plant logistics processes through the design, management and supply of solutions based on Kanban methodology. We focus on ensuring the continuous availability of consumables, fasteners, cutting tools, personal protective equipment (PPE) and other essential consumables for the plant's efficient operation.
Service Features
Our consumables (drawer) control system is designed to optimize the management and replenishment of materials in the industry. We offer a comprehensive solution that includes:
- Customized Locations: We size and assign specific locations for each consumable reference according to your project needs.
- Software Integration: We implement a software solution that integrates with your system, allowing to launch automatic orders to TORSESA when a (drawer) reaches its minimum stock.
- Unique Drawer Identification: Each drawer is uniquely identified by barcodes, QR codes, RFID or other technology of your choice, ensuring accurate tracking of consumables.
Service Process
Our process is designed to be efficient and minimize disruptions to your workflow:
- Empty (Drawer) Detection: When a drawer becomes empty, the worker takes it to the designated pickup cabinet.
- Product Scanning: The worker scans the barcode on the drawer, accurately identifying the product and avoiding errors in the order.
- Automatic Order Generation: After scanning, the cabinet releases a door to deposit the empty drawer and automatically generates a replenishment order to TORSESA.
- Rapid Replenishment: We guarantee an efficient replenishment process, usually overnight. Our technicians deliver full drawers with the corresponding consumables.
- Accurate Placement: Using bar code scanning, full drawers are placed in their correct location on the shelves.
- Pickup and Reuse: In the same process, we collect empty drawers for reuse, promoting sustainable practices and reducing waste.
This system allows an automated and accurate management of your consumables, reducing waiting times and avoiding stock ruptures, which translates into greater operational efficiency.
APPLICATION AREAS
1. Fastener management at the workstation
In fastener management, a Kanban system can be used to organize and control the inventory of fasteners and other fasteners at the workstation. By implementing a Kanban board, operators can visualize the quantity of fasteners on hand, identify when replenishment is necessary and avoid shortages or excess inventory. This not only improves production efficiency, but also reduces the time spent searching for parts and ensures that the necessary items are always on hand.
2. Cutting tools for the aerospace industry
In the aerospace industry, where precision and quality are critical, Kanban can be used to manage cutting tool inventory. A Kanban system allows production teams to monitor tool usage, schedule maintenance and replenish needed tools in a timely manner. This ensures that the right tools are available when needed, minimizing downtime and ensuring that quality standards are met in the manufacture of aircraft components.
3. Abrasives for large metallurgical industries
In large metalworking industries, abrasive management is crucial to maintain efficiency in manufacturing processes. A Kanban system can help control abrasive inventory, allowing operators to visualize available stock and schedule replenishment effectively. This not only optimizes material usage, but also ensures that cutting and finishing processes run without interruption, improving overall plant productivity.
ALCANCE DEL SERVICIO
Optimization of internal plant logistics processes through the design, management and supply of solutions based on Kanban methodology. We focus on ensuring the continuous availability of consumables, fasteners, cutting tools, personal protective equipment (PPE) and other essential consumables for the plant's efficient operation.
Service Features
Our consumables (drawer) control system is designed to optimize the management and replenishment of materials in the industry. We offer a comprehensive solution that includes:
- Customized Locations: We size and assign specific locations for each consumable reference according to your project needs.
- Software Integration: We implement a software solution that integrates with your system, allowing to launch automatic orders to TORSESA when a (drawer) reaches its minimum stock.
- Unique Drawer Identification: Each drawer is uniquely identified by barcodes, QR codes, RFID or other technology of your choice, ensuring accurate tracking of consumables.
Service Process
Our process is designed to be efficient and minimize disruptions to your workflow:
- Empty (Drawer) Detection: When a drawer becomes empty, the worker takes it to the designated pickup cabinet.
- Product Scanning: The worker scans the barcode on the drawer, accurately identifying the product and avoiding errors in the order.
- Automatic Order Generation: After scanning, the cabinet releases a door to deposit the empty drawer and automatically generates a replenishment order to TORSESA.
- Rapid Replenishment: We guarantee an efficient replenishment process, usually overnight. Our technicians deliver full drawers with the corresponding consumables.
- Accurate Placement: Using bar code scanning, full drawers are placed in their correct location on the shelves.
- Pickup and Reuse: In the same process, we collect empty drawers for reuse, promoting sustainable practices and reducing waste.
This system allows an automated and accurate management of your consumables, reducing waiting times and avoiding stock ruptures, which translates into greater operational efficiency.
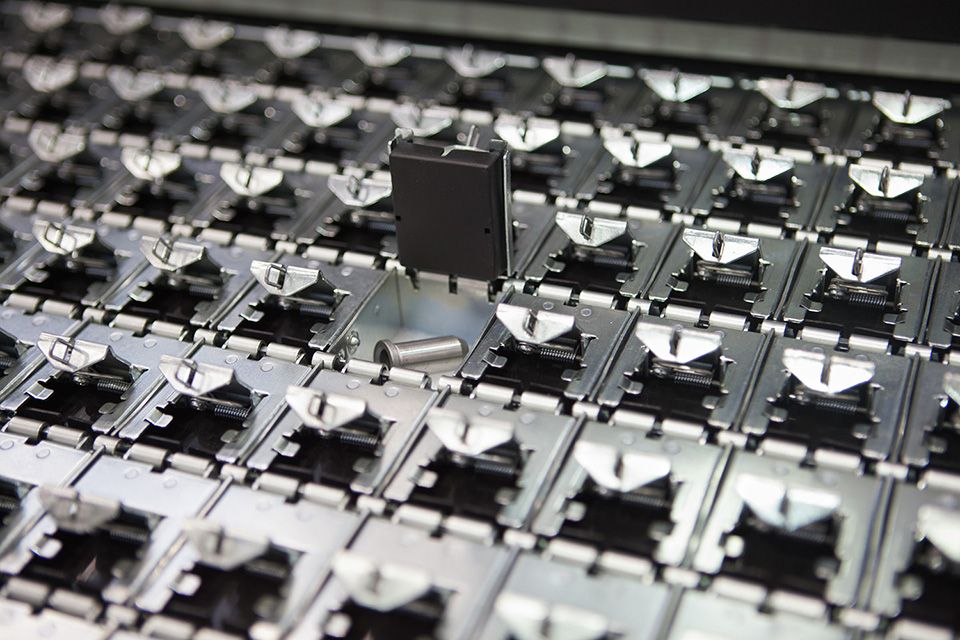
Áreas de Aplicación
1. Fastener management at the workstation
In fastener management, a Kanban system can be used to organize and control the inventory of fasteners and other fasteners at the workstation. By implementing a Kanban board, operators can visualize the quantity of fasteners on hand, identify when replenishment is necessary and avoid shortages or excess inventory. This not only improves production efficiency, but also reduces the time spent searching for parts and ensures that the necessary items are always on hand.
2. Cutting tools for the aerospace industry
In the aerospace industry, where precision and quality are critical, Kanban can be used to manage cutting tool inventory. A Kanban system allows production teams to monitor tool usage, schedule maintenance and replenish needed tools in a timely manner. This ensures that the right tools are available when needed, minimizing downtime and ensuring that quality standards are met in the manufacture of aircraft components.
3. Abrasives for large metallurgical industries
In large metalworking industries, abrasive management is crucial to maintain efficiency in manufacturing processes. A Kanban system can help control abrasive inventory, allowing operators to visualize available stock and schedule replenishment effectively. This not only optimizes material usage, but also ensures that cutting and finishing processes run without interruption, improving overall plant productivity.
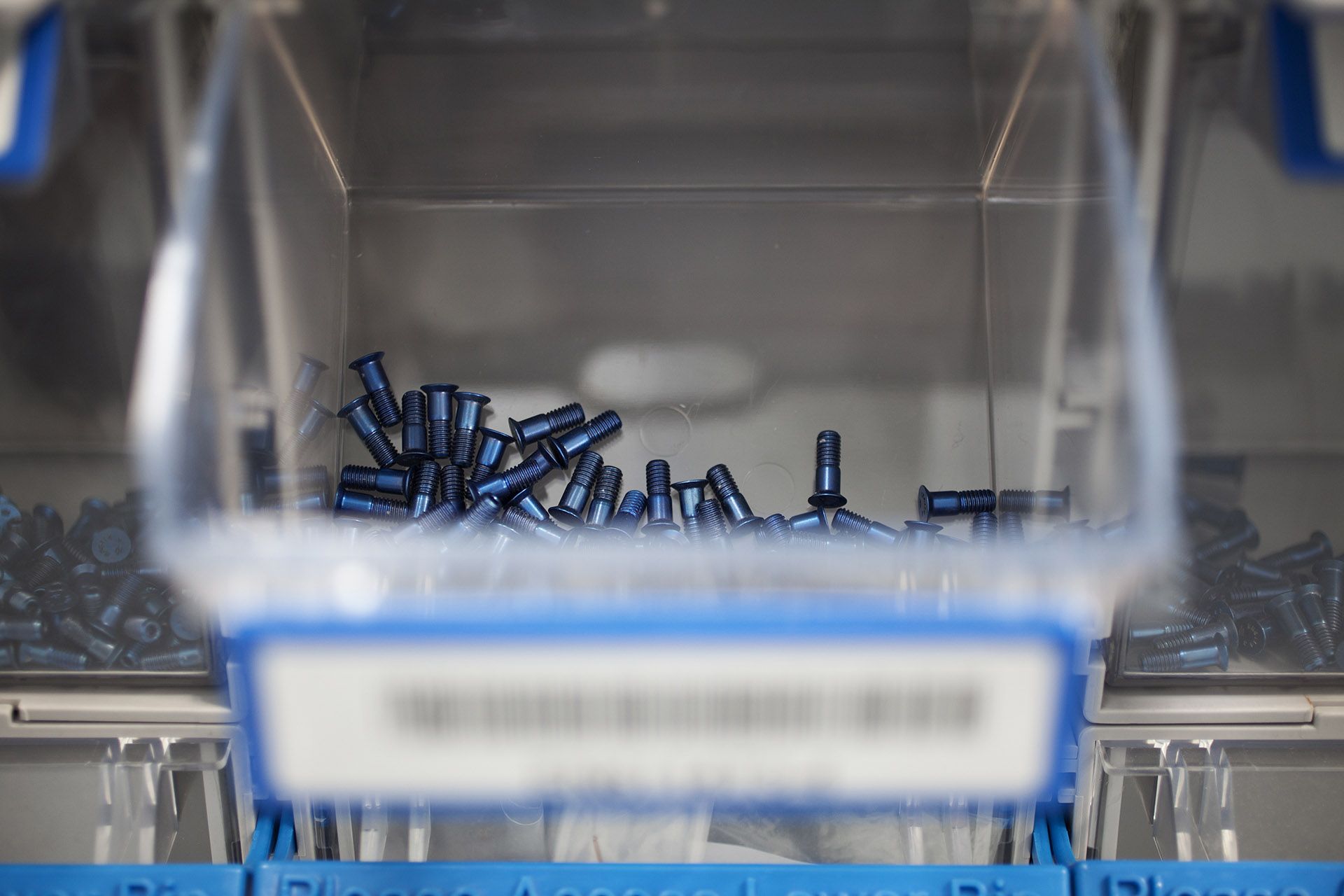
BENEFITS
-
Efficiency
Purchase order generation and content identification.
Replenishment and waiting time reduction.
Inventory and waste reduction. -
Availability
Consumables and tools always available when needed.
-
Robust processes
Adaptation of the solution to the needs of each plant or production line.
Greater visibility of material flow and resource usage. -
Productivity
Production quality and waste elimination thanks to efficient logistics.
-
Safety
Continuous availability of appropriate PPE and tools, reducing the risk of accidents.
BENEFICIOS
-
Efficiency
Purchase order generation and content identification.
Replenishment and waiting time reduction.
Inventory and waste reduction. -
Availability
Consumables and tools always available when needed.
-
Robust processes
Adaptation of the solution to the needs of each plant or production line.
Greater visibility of material flow and resource usage. -
Productivity
Production quality and waste elimination thanks to efficient logistics.
-
Safety
Continuous availability of appropriate PPE and tools, reducing the risk of accidents.
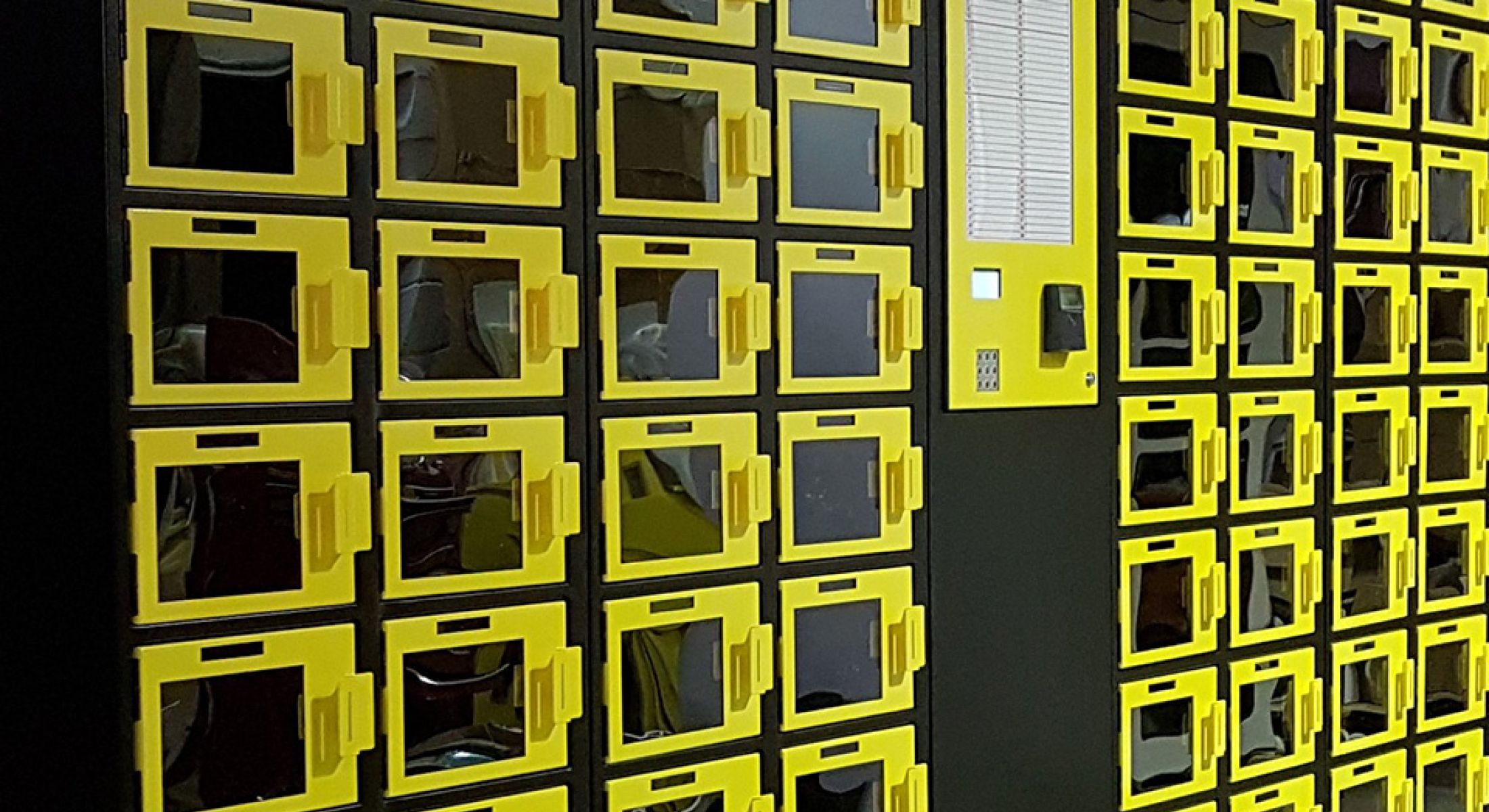
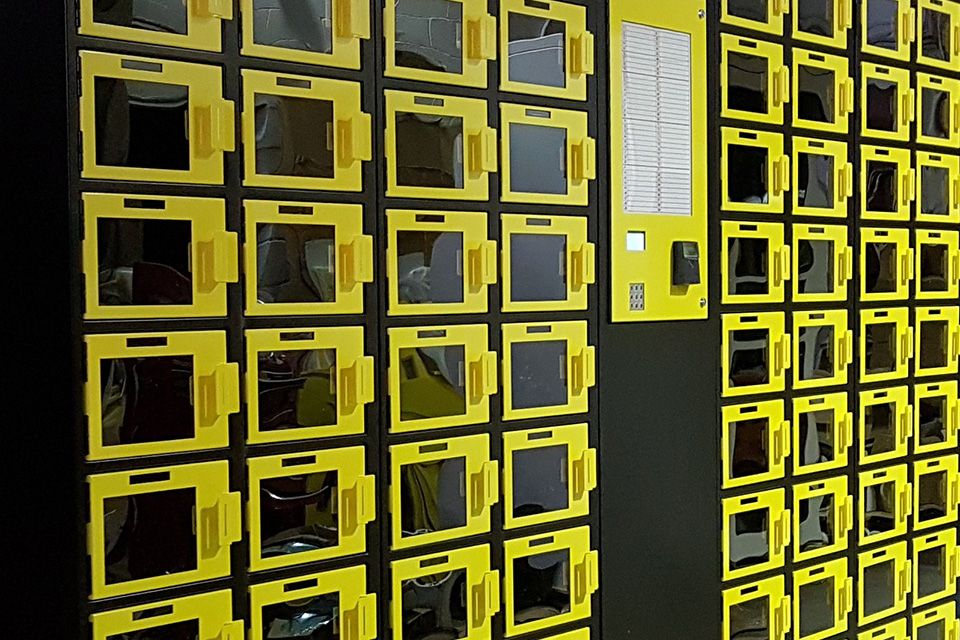